
Getting an old industrial machine (this one I got is a 1998) means there is lots of capability, heavy, rigid, plenty of power, full enclosure, flood coolant, tool changer, 4 axis. On a CNC it is two lines of code to create the shape, then repeated 8 times with the origin translated - so I made two full sets of the jaws. For example I made some two piece jaws for a big 3J chuck - I know it is possible to generate a good approximation of the scroll teeth on the back of the jaw using a manual mill, but it is a lot of work. Even though I'm a total beginner, it is not difficult to get to the point that I'm doing things that would be much harder to do on one of the manual milling machines. I am steadily building ever more involved programs. I appreciate that the real power is in doing the solid model and programming too paths, but as a manual machining guy for many years, pretending it is a manual machine, except instead of cranking a handle, I just send a line of code - is really awesome. There are good post processors for my machine, DX32 - but I have simply stuck with coding directly. I picked up a Bridgeport VMC 1000 for $5000 CAD, it needed a bit of work, but not too much just to make chips (beware that machining is an endless way to suck a little more money, one tool at a time).

A PCNC1100 package would have added another $2K but the deciding factor was available space.Ĭr234 - what you want to do is possible. The package that I chose was around $14K at the time, probably closer to $16K now. The 440 wasn't available yet but I still would have gone the 770 route anyway. The PCNC1100 is the next step up but you are getting into a industrial machine price range. Adding bells and whistles can triple those prices. A more substantial machine would be the Tormach PCNC440starting at around $5K or the PCNC770 for $8K.
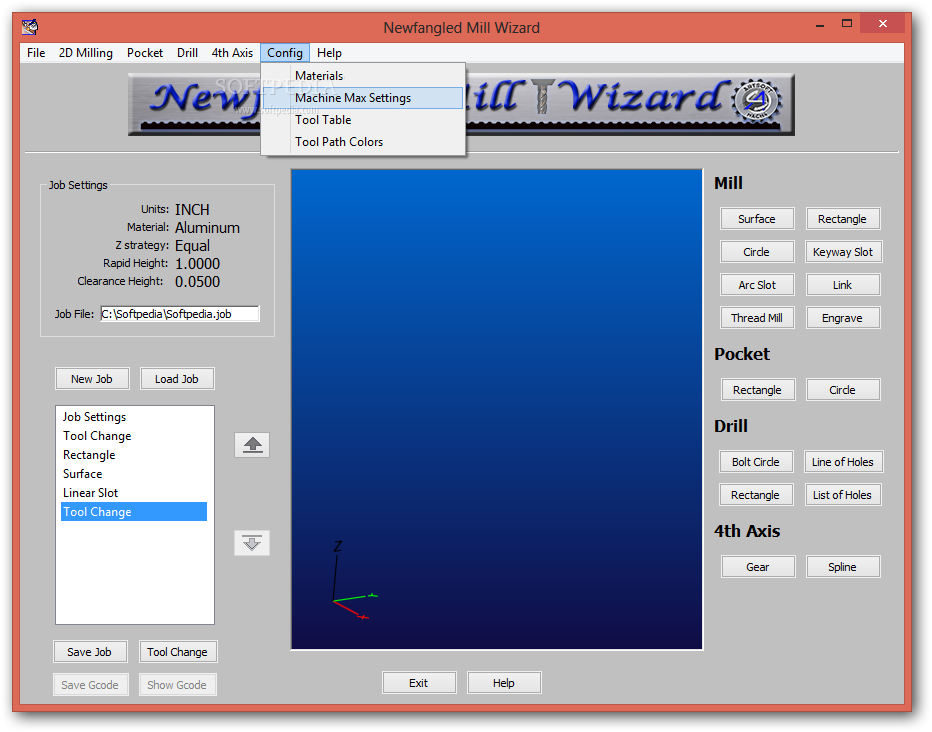
You can buy several new machines like the Sherline for around $2K bit they are light duty. What your expectations regarding performance will govern the decistion about how much machine is needed. A CAM program alone can import 3rd person solid models and ceate G code to make copies.Īs to the actual hardware, there are basically three ways to go convert a manual machine to CNC, buy a used CNC, or buy a new CNC. A 3D modeling program, along with a CAM program will permit creating complex shapes in two or three dimensions.
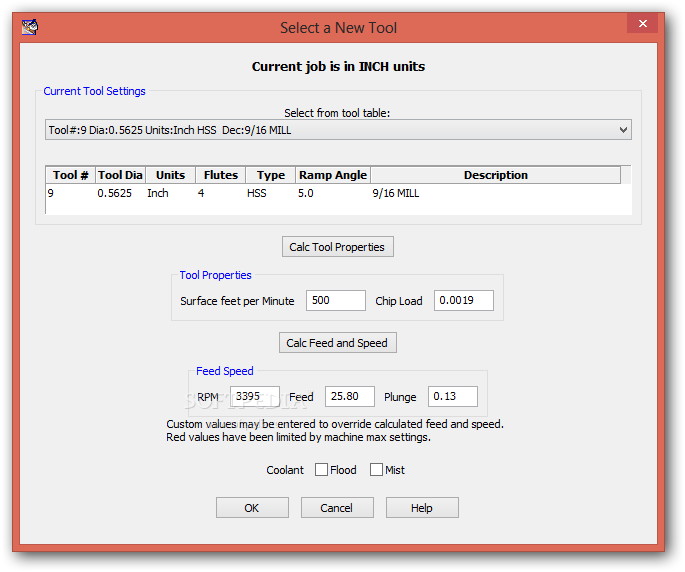
A 2D CAD package will facilitate creation of the programs. This will enable one to cut simple arcs, move in straight lines, drill patterned holes. G code is a fairly simple language, at least for rudimentary programs and one can create G code programs with a simple text processor like Wordpad.
